Backhoe loaders are essential equipment in construction, mining, and agriculture. To ensure their efficiency, safety, and durability, it is crucial to perform proper and periodic maintenance. In this ultimate guide, we will explore the different types of maintenance that can be carried out on a backhoe loader, their importance, and the best practices to keep your machinery in optimal condition.
1. Preventive Maintenance
Preventive maintenance is performed on a scheduled basis to prevent unexpected failures and extend the equipment’s lifespan. This type of maintenance includes:
- Oil and filter changes: Regularly checking and changing the engine oil, hydraulic oil, and air filters is crucial to avoid residue buildup that could affect engine and hydraulic system performance.
- Lubrication of moving parts: Joints, pins, and bushings must be well-lubricated to reduce wear and improve component mobility.
- Cooling system inspection: It is important to clean the radiator and check coolant levels to prevent engine overheating.
- Electrical system inspection: Cables, connections, and batteries should be checked to prevent electrical failures.
- Brake and transmission system check: Fluid levels, discs, and brake pads should be inspected to ensure the backhoe loader’s proper functioning.
Don’t forget, we also offer a wide range of spare parts for heavy machinery, so feel free to inquire about any replacement needs you may have. Just click on contact us.
2. Corrective Maintenance
This type of maintenance is carried out when the backhoe loader presents failures or breakdowns. It is advisable to act quickly to avoid major damage and costly repairs. Some corrective actions include:
- Repair or replacement of damaged components: Parts such as hydraulic cylinders, hoses, and pumps should be checked and replaced in case of leaks or excessive wear.
- Replacement of structural components: Arms, buckets, and booms can wear out with continuous use and should be regularly inspected.
- Undercarriage inspection: If the backhoe loader uses tracks, their alignment and condition should be checked to avoid mobility failures.
3. Predictive Maintenance
Predictive maintenance is based on continuous monitoring of the machinery’s condition to detect problems before major failures occur. For this, tools and techniques such as:
- Vibration analysis: Helps detect wear or misalignments in key components like the engine and transmission.
- Thermographic inspection: Thermal cameras are used to identify abnormal overheating in electrical or hydraulic systems.
- Oil analysis: Laboratory tests can identify metallic particles in the oil, indicating internal wear.
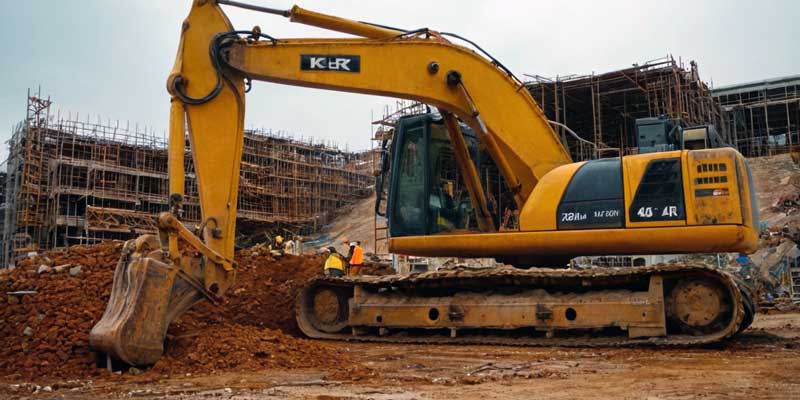
4. Proactive Maintenance
This approach aims to improve the performance of the backhoe loader by implementing enhancements and advanced technologies. Some strategies include:
- Use of telemetry and sensors: These devices allow real-time monitoring of machinery conditions and provide alerts in case of anomalies.
- Optimization of machine use: Training operators to use the backhoe loader efficiently can reduce wear and extend the equipment’s lifespan.
- Software updates: Some modern backhoe loaders have computerized systems that can be updated to improve performance and efficiency.
Proper maintenance of a backhoe loader is key to ensuring its operation and avoiding costly downtime. Implementing a preventive, corrective, predictive, and proactive maintenance plan will maximize productivity and extend the machinery’s lifespan. By following these recommendations, you will ensure that your backhoe loader operates optimally for many years.